Space News & Blog Articles
High-stakes sunshield deployment begins on Webb telescope
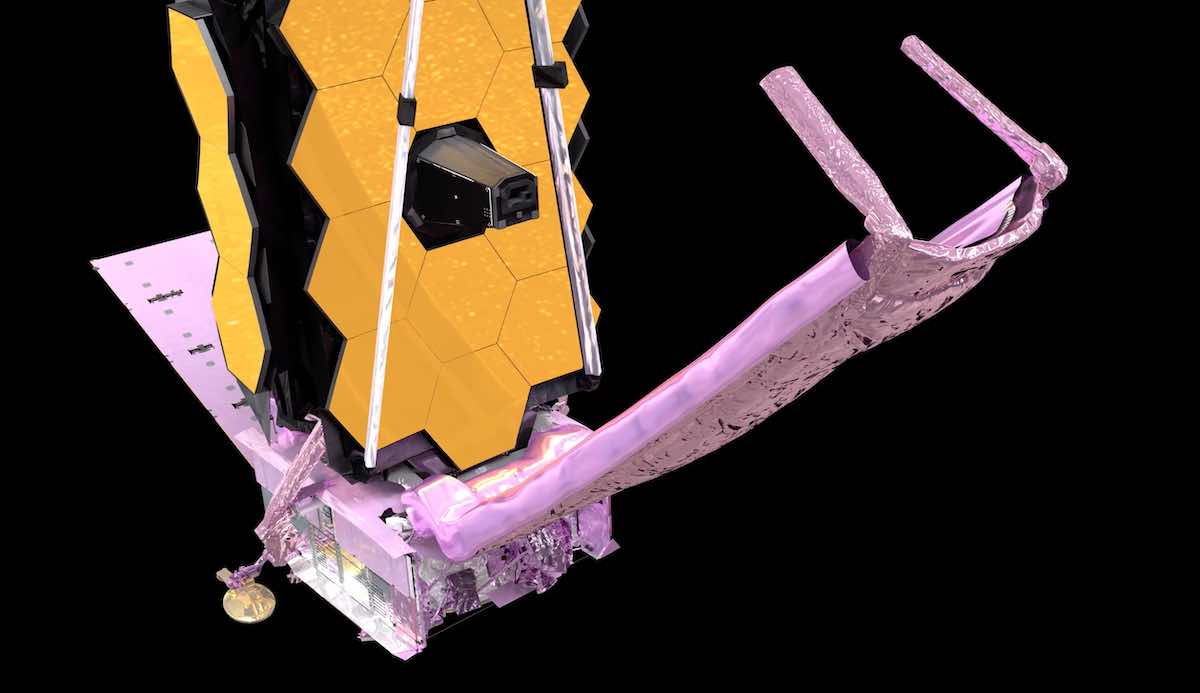
Mission controllers started the risky process Tuesday to unfurl the James Webb Space Telescope’s sunshield, a five-layer thermal barrier necessary to give the observatory infrared vision into the distant universe.
Two large pallets containing the sunshield membranes were folded up on each side of Webb’s primary mirror for launch. Now, with Webb on course toward an observing post nearly a million miles (1.5 million kilometers) from Earth, ground teams are ready to open up the sunshield to its full dimension.
Made of five fragile kapton membranes, each as thin as a human hair, the sunshield will keep Webb’s mirrors, instruments, and detectors in constant shadow, allowing their operating temperature to reach near minus 400 degrees Fahrenheit. Such cold conditions are required to allow Webb to see the faint infrared light from the first galaxies in the universe more than 13.5 billion light years away.
Webb, the largest space telescope ever launched. had to fold up to fit inside the payload fairing of its Ariane 5 rocket for liftoff Christmas morning.
“We built a world-class infrared telescope,” said Mike Menzel, Webb’s mission systems engineer at NASA’s Goddard Space Flight Center. “We built it, we’ve aligned it, we’ve tested it, and proved it worked.”
“Now, we’re going t have to break it up, fold it up, and actually rebuild it on orbit — rebuild it, realign it, retune it and get it to work robotically on orbit. That’s never been done before.”
Most NASA managers and astronomers waiting to use the nearly $10 billion Webb telescope give the same answer about the most stressful moment of the mission: Sunshield deployment.
“The sunshield is one of these things that is almost inherently indeterministic,” Menzel said. “NASA is used to deploying rigid beams on hinges, because they’re deterministic, you can determine how they move.”
Once the sunshield is opened to its full size — with the approximate dimensions of a tennis court — NASA will send commands to open wings on each side of the telescope’s primary mirror, giving the aperture its final diameter of 21.3 feet (6.5 meters). A tripod-like structure with Webb’s secondary mirror must also deploy.
“Given that there are 40 different major deployments, and hundreds of pulleys and wires, the whole thing makes me nervous and will until its fully deployed,” said John Grunsfeld, an astrophysicist, former astronaut, and head of NASA’s science mission directorate from 2012 until 2016, a key period in Webb’s development.
But it’s the sunshield that got the biggest share of Menzel’s attention during the design and testing of Webb.
Menzel compares predicting the behavior of the sunshield layers to guessing what a string will do when you push it on a table top.
“So it is with the membranes of the sunshield,” he said. “So we can’t really predict their shape, but we can constrain it. “We can try to prevent it from going in places that we don’t want it to go, places where it could snag or tear, or maybe impede the deployment of other members.”
If everything goes according to plan, the timeline to deploy and tension the sunshield will take five days. But mission planners have flexibility in that schedule, and could decide to postpone or defer some steps to look at data in the event of a problem.
The first day of sunshield deployment apparently went off without a hitch. NASA said the two sunshield pallets lowered into position in front of and behind the telescope Tuesday. The two pallets extend 69.5 feet (21.2 meters) tip to tip.
The pallets, called Unitized Pallet Structures, contain the five kapton sunshield layers carefully folded and stowed by engineers at Northrop Grumman, NASA’s prime contractor for the Webb mission.
“Webb is beginning to resemble the form it will take when it is fully deployed – now that the mission operations team has successfully deployed and latched into place the observatory’s forward and aft Unitized Pallet Structures,” NASA said in an update late Tuesday.
The forward pallet lowered first, with its unfolding finished at around 1:21 p.m. EST (1821 GMT) Tuesday, NASA said. The next step was the unfolding of the aft pallet, which was confirmed fixed in its deployed position at around 7:27 p.m. EST (0027 GMT).
It took around 20 minutes to deploy the forward pallet, and 18 minutes to move the aft pallet, NASA said. But the process included additional steps spanning several hours, allowing ground teams to monitor structural temperatures and maneuver the observatory with respect to the sun to provide optimal thermal conditions for the deployments, the agency said.
Ground teams also turned on heaters, activated release mechanisms, and verified software configurations before latching the pallets into place, NASA said. Mission control for Webb is at the Space Telescope Science Institute in Baltimore, Maryland.
“Each deployment usually involves a bunch of motor checks, small moves to verify motor performance, heating of anything that is too cold, etc,” said Keith Parrish, Webb’s commissioning manager at NASA. “We also have to power on and configure our deployment electronics, which controls the whole show. “
The deployment of the sunshield pallets followed a smooth first three days in space for Webb.
The three-story-tall observatory launched from French Guiana on Christmas morning atop a European Ariane 5 rocket. The launcher delivered Webb to a bullseye point in space, and the spacecraft unfurled its solar array, completed two mid-course correction burns, and opened its high-gain antenna over the last few days.
Webb has passed the orbit of the moon en route to an operating orbit around the L2 Lagrange point, a gravitational balance point nearly a million miles beyond the night side of the Earth. The spacecraft is scheduled to arrive in its halo orbit around L2 in late January.
Next up is the raising of Webb’s Deployable Tower Assembly, which moves the telescope away from the spacecraft. The telescope structure contains Webb’s 18 hexagonal primary mirror segments and four infrared instruments mounted in a carbon composite module built to withstand the observatory’s cryogenic operating temperature.
That is scheduled to occur Wednesday.
“All of the material for the sunshield is actually stowed in that area, or some of it is, so we need to get the telescope up away, so that will allow us to pull that material out,” Parrish said.
The next big event, tentatively set for Thursday, will be the opening of protective covers over the sunshield membranes. The five layers took a month to carefully, and manually, stow inside the pallets, akin to the way a parachute is packed before a skydive. extension of two booms from each side of the observatory.
“It needs to be folded perfectly so that it unfolds and deploys perfectly, without snags, without any tangles,” said Krystal Puga, Webb’s lead spacecraft systems engineer at Northrop Grumman.
Launch restraints will disengage to allow the covers to roll off the top of the sunshade. Another deployment on tap Thursday, if schedules hold, is the release of Webb’s aft momentum tab, a rear flap that balances the pressure from solar light pressure on the sunshield, helping keep the observatory stable as it goes around the sun in lock-step with Earth.
Then, as soon as Friday, two booms will extend from each side of Webb. With the assistance of deployment motors, the structural support booms will pull the five sunshade membranes out into their distinctive diamond shape.
It all happens slowly, with sensors across the observatory tracking how the sunshield opens. Ground controllers can pause in between steps to ensure everything is working as designed.
Each layer of the sunshield is slightly different in size and shape, created using thermally bonded sections of kapton with around 10,000 seams, according to Puga. There are reinforcement strips, or rip stops, to contain any tears or holes, and metallic ribbons giving the kapton some structural support.
The sunshield membranes are coated with aluminum, and two of the outermost layers are treated with silicon, giving the skin-like material a purple hue.
Webb has 344 devices that must work exactly as intended. Of those, 107 are membrane release devices, non-explosive actuators that pin the sunshield in place for launch.
In total, the mission’s deployment sequence relies on 140 release mechanisms, 70 hinge assemblies, eight deployment motors, 400 pulleys, and 90 cables running a quarter-mile in length. There are also an array of bearings, springs, and gears to transform Webb from its launch to operational configuration.
With the sunshield in its diamond shape, covering an area the size of a tennis court, Webb controllers will send commands for the observatory to tension each of the five layers over two days — currently planned on Jan. 1 and Jan. 2.
“Once we get the sunshield out, that’s great, but then we have to sort of tighten it up,” Parrish said. “All five layers have different points around them where they’re connected up, and then we’ll pull on cables in each one of those corners to actually tighten up the sunshield.”
“The very last step is super important,” Puga said. “We need to tension all of the membranes using a series of pulleys and cables to create the separation between each of the five layers.”
The tensioning will separate each of the five ultra-thin kapton membranes, spacing them a few inches at the center and a few feet at the outermost edges. The tapered spacing helps allow heat from the sun to reflect between the layers, and eventually radiate back into space.
If there’s a minor tear or snag that only affects a small part of the sunshield, Webb could still accomplish many of its science goals. Three of the telescope’s instruments — the U.S.-made Near-Infrared Camera, the European Near-Infrared Spectrograph, and the Canadian Near Infrared Imager and Slitless Spectrograph — are tuned to observe the universe in near-infrared wavelengths closer to visible light.
They’re designed to work at temperatures around minus 388 degrees Fahrenheit, or 40 degrees above absolute zero. Those instruments could still be sensitive to faint infrared light if they’re a few degrees warmer, Menzel said.
Webb’s Eurpoean-built Mid-Infrared Instrument, designed to detect longer light waves, needs to be chilled 33 degrees colder than the others. A cryocooler pumping cold helium gas into the instrument will get the mid-infrared instrument to its prescribed temperature, but any deficiencies in the observatory’s sunshield might jeopardize MIRI’s science goals, which are aimed at detecting light from the universe’s oldest galaxies, and peering into star-forming dust clouds opaque at shorter wavelengths.
But any large-scale malfunction would be difficult for Webb to overcome.
“All of these single-point failures, all of these deployment mechanisms, all of the things the have to go right to make a telescope, there’s no halfway stage,” said Mark McCaughrean, a senior science advisor at ESA and an interdisciplinary scientist with observing time on Webb in its first year of operations.
“If the sunshield only half-deploys, the telescope never gets cold, the instruments won’t turn on,” McCaughrean said. “So that’s the nerve-wracking time — that first month — and after that the five months of cool down and commissioning, and then we can start doing the science.
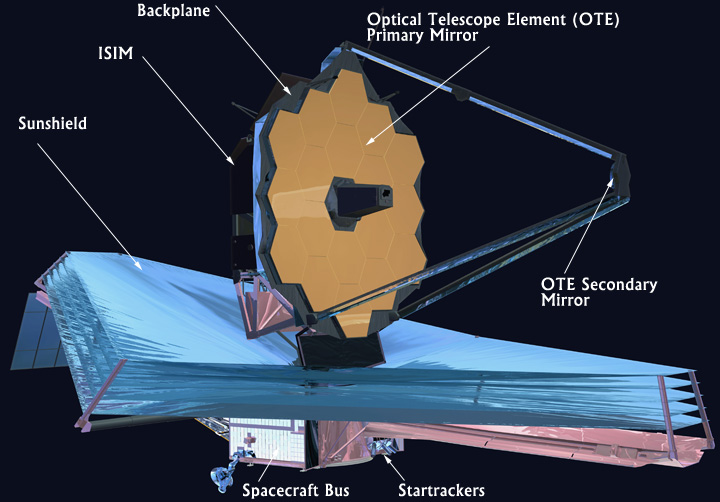
“There’s never 100% certainty on anything like this,” McCaughrean said before the launch. “And if it fails, I think it would be an absolute catastrophe for astronomy, for space science. There’s been a lot of talk about this mission for many years, and if it does fail somewhere along the way, there will be a reckoning.
“But that’s why we feel so much pressure to have done the right job before we launched it,” he said.
Assuming no delays with the sunshield deployment, Webb’s ground team will turn their attention to moving elements of the telescope into place next week.
First will come the deployment of the secondary mirror, currently planned for Jan. 4, which focuses light from the primary mirror into the telescope’s internal focal plane, ultimately leading to Webb’s instrument detector arrays.
Then the two wings of the primary mirror will fold into place Jan. 6 and Jan. 7, according to Webb’s preliminary flight plan.
Each wing holds three of Webb’s six-sided mirror segments, with 12 mirrors fixed to the primary mirror’s central structure.
All along the way, we’re doing a lot of releases and (actuating) launch locks,” Parrish said. “We release our cryogenic cooler assembly, we have some additional radiators that we have to deploy … I don’t want to call them small deployments, but there are other deployments that don’t quite make the headlines like the sunshield does.”
Once the mirrors are in place, optical engineers will begin unlocking each segment from its launch restraint. Tiny motors behind each mirror can move it back and forth, up and down, left and right, and even slightly bend the mirror segment to bring the entire telescope into sharp focus.
“That’s a very tedious process,” Parrish sad. “They only move them a really, really tiny bit each time.”
Once Webb is in orbit around L2 next month, ground controllers will continue aligning the telescope, switch on and calibrate the instruments, and ready the observatory for science operations. All this work will occur in parallel to the natural cool-down of the telescope to cryogenic temperatures.
Engineers devised numerous emergency procedures to deal with a problem during Webb’s intricate deployment sequence. They range from options as simple as switching to a backup drive, where possible, to backing up a motor and re-attempting a deployment.
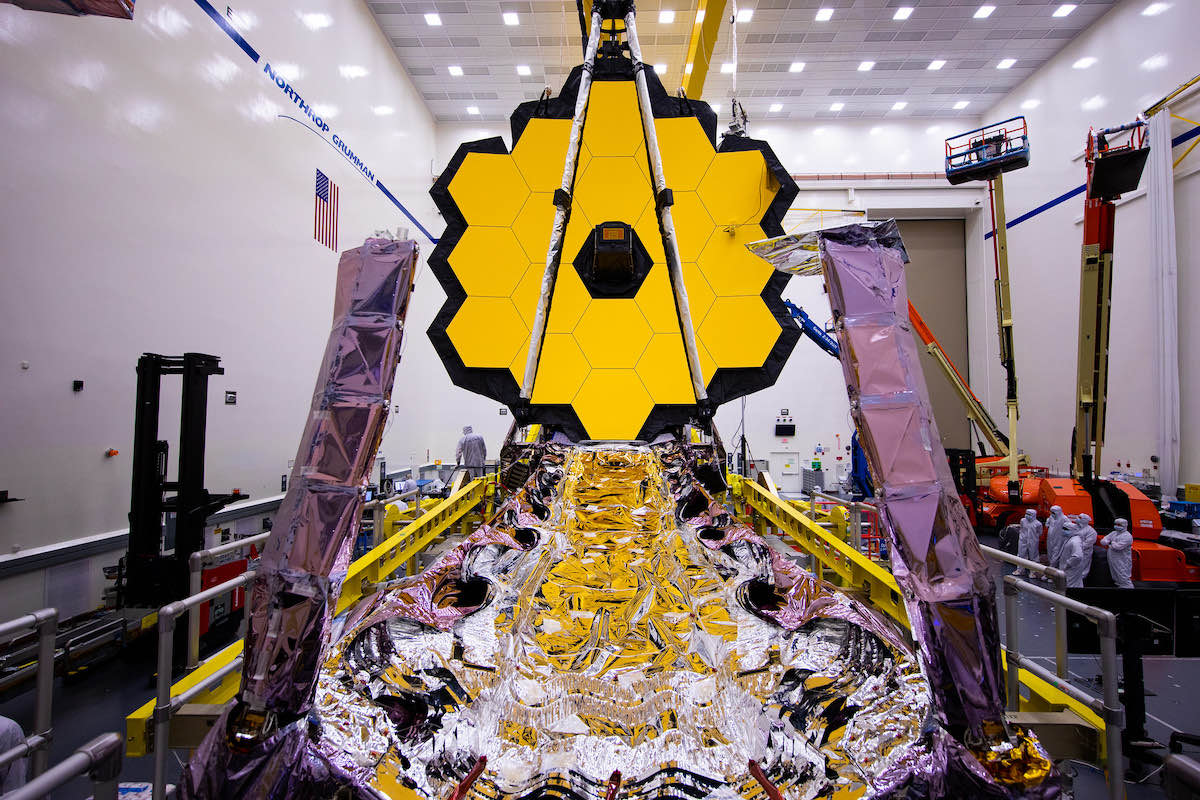
The last-ditch options? Teams can shimmy or twirl Webb in space, or subject the observatory to fire and ice.
“A shimmy is our ability to shake Webb a little bit using its on-board propulsion system,” Parrish said. “We can actually impose some shaking into that system.
“We can also twirl the observatory, which means we can spin it at a rate to where we can put some static forces and help put some loading on an are that may be a little stubborn.
“We also have the ability to use the attitude control system, specifically the propulsion system, to be able to move Webb back and forth rapidly, so we can heat and cool a specific area that may be giving us some trouble … We call the back and forth fire and ice.
“If we’re using those tools in our toolbox, we’re not having the best of days,” Parrish said.
With Webb heading four times farther than the moon, there’s no way for astronauts to visit for repairs, like space shuttle crews serviced the Hubble Space Telescope. It also wasn’t designed for robotic servicing.
Grunsfeld, who flew to Hubble on three shuttle repair missions, said he tried to implement a late design change on Webb to make it more amenable to servicing.
“When I took over management of the science mission directorate, and by extension the James Webb Space Telescope, one of my first responses was let’s put a little grapple fixture — really small — and some targets on the James Webb, just in case we have to run it down and give it a little shake to try and deploy it.
“And I got enormous push back,” Grunsfeld said. “The design for James Webb was incredibly mature, basically finished, and mass was a concern. Even though what I proposed was half a kilogram, they said, ‘No, we can’t add any mass.'”
And there are no cameras on-board to give ground teams a visual perspective on how things are going. But any camera in a position to observe the telescope’s deployment would need to be on the “cold side” off the observatory, requiring them to be armored to withstand the super-cold, shadowed conditions.
And warmth put out by the camera electronics could interfere with Webb’s science observations.
“Anything that’s hot within the field of view of the telescope will ruin it,” Grunsfeld said.
“We have lots of little micro-switches to tell us what the configuration is exactly, so we don’t necessary need cameras. We can image it on a computer,” Grunsfeld said. “While I agree, totally, that that’s true, being visual animals, we like to see things, but we will have those animations.”
This email address is being protected from spambots. You need JavaScript enabled to view it. the author.
Follow Stephen Clark on Twitter: @StephenClark1.
When you subscribe to the SpaceZE News Feed, we will send you an e-mail when there are new updates on the site so you wouldn't miss them.