Space News & Blog Articles
Webb’s fate hinges on high-risk sunshade, mirror deployments
STORY WRITTEN FOR CBS NEWS & USED WITH PERMISSION
If you want to see the faint, stretched-out light from the first stars and galaxies that began shining at the end of the cosmic dark ages a few hundred million years after the Big Bang, you’re going to need a big telescope. But not just any big telescope.
You’re going to need to put it in space where it will have to operate at a few degrees above absolute zero to register the exceedingly faint infrared traces of that bygone era, detecting light that has been stretched out by the expansion of space itself over nearly 14 billion years.
To do that, you’ll have to equip the observatory with a tennis court-size kite-shaped sunshade, made up of five membranes the thickness of a human hair separated and pulled taught by scores of motor-driven stainless steel cables routed through dozens of pulleys.
You’ll need to choose materials for the observatory’s structure that will retain their shape and size across enormous temperature gradients.
Then you’ll have to fold it all up so it can be crammed into the nosecone of a rocket and fired a million miles into space, hoping the vibrations and ear-splitting sounds of launch don’t dislodge a critical component so it can unfold itself, align its optics to nanometer precision and bring that feeble light to a razor-sharp focus.
That’s the Christmas holiday challenge facing the $9.8 billion James Webb Space Telescope, the successor to the 31-year-old Hubble. It is by far the most sensitive, technologically challenging — and expensive — science satellite ever built.
The spacecraft, encapsulated inside a protective nose cone atop a European Space Agency-provided Ariane 5 rocket, was rolled to the launch pad in Kourou, French Guiana, Thursday. Launch is targeted for 7:20 a.m. EST Christmas Day, weather permitting.
Once on its way, it will take a full month for the telescope to unfold like a high-tech origami, deploying its solar array, antennas, radiators, its segmented primary mirror, its secondary mirror and the complex, fragile sunshade that is so essential to success.
Another two months beyond that will be needed to carefully align the optics while the telescope continues a slow cool down to near absolute zero and then another three months or so to check out and calibrate Webb’s instruments.
And then, more than 20 years after it was first proposed, years behind schedule and billions over budget, JWST will finally be ready to take center stage on the high frontier, carrying the hopes and dreams of thousands of engineers and astronomers around the world.
“This is a high-risk and a very high-payoff program,” said NASA Deputy Administrator Pam Melroy, a former space shuttle commander. “We’ve done everything we can think of to make Webb successful. And now we just need to go do it.”
LOOKING FOR THE OLDEST STARLIGHT THERE IS
Unlike Hubble, which was placed in low-Earth orbit where space shuttle astronauts could make service calls, JWST is headed for Lagrange Point 2 on the other side of the Moon where the gravity of Sun, Earth and Moon are in balance, allowing the telescope to remain in place with a minimum of propellant.
Well beyond the reach of spacewalking repairmen, L2 offers an ideal place for Webb to chill out for its epic quest to peer back in time to the end of the so-called dark ages, when the the blazing light of the first stars burned off the hydrogen fog of creation to travel freely through space.
“It’s an infrared telescope,” said Paul Geithner, JWST’s technical project manager. “The main reason it was conceived in the first place was to see the end of the cosmic dark ages. And if you want to see objects from that epoch, the ultraviolet and the visible light they emitted so long ago has been red shifted all the way into the infrared spectrum.
“Infrared light is heat radiation. So if you want an infrared telescope to be exquisitely sensitive, first you put in space (and) besides putting in space, you need it to be super cold so that it’s not blinded by its own thermal emissions.”
Operating at L2, JWST will be less affected by the infrared background close to Earth and the scattered and re-emitted infrared light from dust in the equatorial plane of the solar system. “We need to be colder than 60 Kelvin so that we’re not limited by our own temperature,” Geithner said.
The hot side of JWST – the spacecraft bus and the bottom layer of the sunshade – will experience temperatures of nearly 230 degrees Fahrenheit. On the dark side, just beyond the fifth and uppermost layer of the sunshade, the temperature will be close to minus 390 degrees.
“That’s a huge, huge temperature differential, driven totally by these five layers on the sunshield (and) each layer is about the thickness of a human hair,” project manager Bill Ochs said in an interview.
Thirty minutes after liftoff, JWST will separate from the Ariane 5’s upper stage. Moments later, the observatory’s solar array will deploy to begin recharging on-board batteries and 12 hours after that, a thruster firing is planned to fine-tune the trajectory to L2.
Passing the moon’s orbit the day after Christmas, JWST will deploy its high-gain antenna and aim it toward Earth, giving flight controllers a high-speed data link.
Three days after launch, the two pallets holding the stowed sunshade membranes will unfold, dropping into place on either side of the Optical Telescope Element-Integrated Science Instrument Module, or OTIS. The OTIS is the actual telescope, its mirrors and instruments mounted in a carbon composite framework.
To achieve the required operating temperature, a telescoping “deployable tower assembly” will move the OTIS 48 inches away from the spacecraft’s support section, or bus, which houses relatively warm communications, thermal control and computer gear, along with the observatory’s propulsion and electrical power systems.
DEPLOYING A 1-MILLION SPF SUNSHADE
With the DTA extended, the stage will be set for the make-or-break deployment of the sunshade’s five Kapton membranes.
“The solar array deploying, the high gain antenna gimbal deploying and working are kind of standard stuff on a spacecraft and not that uncommon,” Geithner said. “And we’ve got to deploy that tower to separate the telescope from the bus to isolate it mechanically and thermally. That’s a little new, but it’s a fairly straightforward ball-screw mechanism.
“But yeah, the sun shield is where so much of the deployment risk exists because that’s where so many of the single point failures exist. And it’s just complicated.”
With the sunshade pallets already deployed fore and aft of the extended optics assembly, launch restraints will be released and protective covers rolled back to either side of the folded sunshade membranes. Two mid booms at right angles to the pallets then will extend and motor-driven cables will pull the stowed membranes out into a kite-like shape.
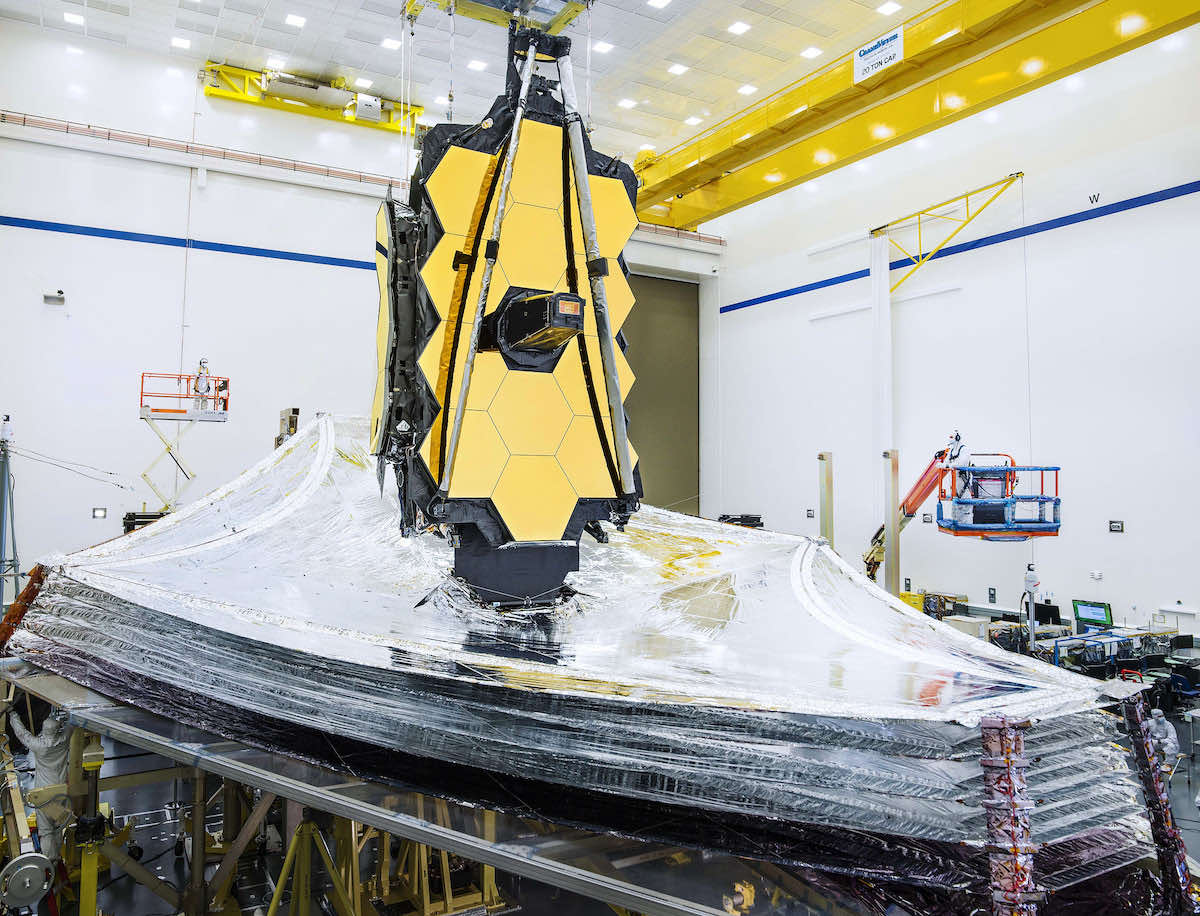
As the cables tighten, the layers will be separated and tensioned as required to ensure a slight gap between each taut layer. Near the center of the shade, the gap is as small as one inch to five inches while at the outboard corners, the separation is about a foot to facilitate heat flow. Fully deployed, the sunshade will measure 69.5-by-46.5 feet.
“The sunshield alone has 90 cables in it, that if you strung them end to end would be almost a quarter mile in length,” Geithner said. “And that’s for pulling out the membranes and tensioning them. … And, of course, we have 107 little non-explosive actuator devices, membrane release devices, that basically pin the membranes down and the covers over them for launch.”
Except for the booms, the sun shield is made up of “floppy things, and they’ll just float around in zero G and you’ll get a tangled mess if you don’t deterministically control them as much as possible,” he said.
“And so we have many little devices to constrain and ensure that all these cables and membranes and such don’t just flop around randomly and snag on something. That’s just where so much of the deployment risk is because it’s a lot of parts. They’re simple mechanisms, but there are a lot of them, and they all have to work.”
Ochs said the sunshade deploy sequence was designed to be “slow and deliberate” to give engineers time to evaluate each step in the procedure. While NASA can’t send an astronaut repair crew to the telescope, engineers have developed contingency plans to coax open jammed mechanisms.
“Whereas the mechanisms themselves are not redundant, the electronics that drive those mechanisms have redundant sides, we can go to the redundant side if there was a problem there to try to deploy it,” he said. “And then if we get to a situation where let’s say something stuck, we can shake the spacecraft using its attitude control system. We call it the ‘shimmy,’ where you can go back and forth at various frequencies and cause it to kind of shake something loose.”
Another procedure, known as the “twirl,” was developed to spin the observatory at various speeds, again to “shake something loose.”
“You can also back things up and have them start again,” Ochs said. “So if you need to back it up and give it another shot, you can do that. We’ve exercised many of these things in some of our rehearsals already, so we have these tools to help us along as we go through all these deployments.”
But what happens if there’s a serious snag, layers remain in contact with each other or membranes are torn?
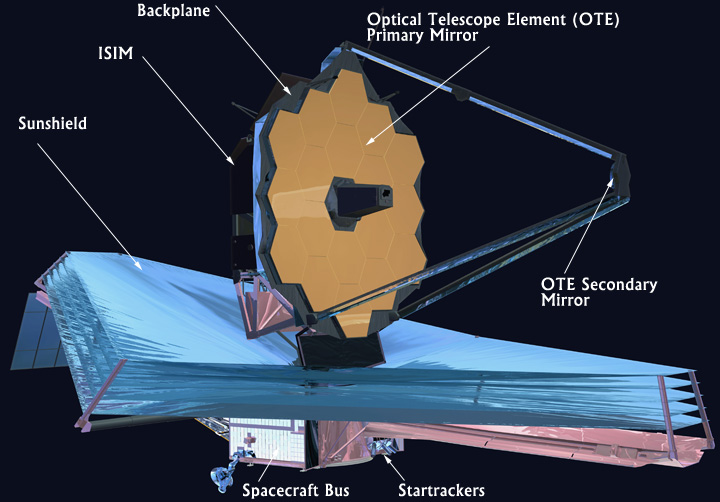
Depending on the degree of thermal degradation, JWST’s three passively-cooled near-infrared instruments — the Near-Infrared Camera, or NIRCam; the Near-Infrared Spectrograph, or NIRSpec; and the Near InfraRed imager and Slitless Spectrograph/Fine Guidance Sensor, or NIRISS/FGS — should still be able to collect valuable data.
All three use 4-megapixel mercury-cadmium-telluride detectors to register infrared wavelengths between 0.6 and 5 microns. All three are designed to operate best at temperatures just below 40 Kelvin (degrees above absolute zero), but they would still work if slightly warmer.
JWST’s fourth instrument, the Mid-Infrared Instrument, or MIRI, uses 1-megapixel arsenic-doped silicon detectors to pull in wavelengths between 5 and 28 microns. It is designed to operate below 7 Kelvin, relying on a sophisticated cryocooler to pump cold helium gas from the spacecraft bus to the MIRI’s detectors.
The instrument has built-in margin, but “the real question is will the heat load on the Mid-Infrared Instrument be so high that the cryo cooler can’t overcome it? I think we’re still okay,” Geithner said. “Worst case, maybe we wouldn’t have a mid-infrared instrument. But you’d still be able to do some near-infrared science. You’d still have a mission, but it would be degraded.”
Ochs is confident the sunshade will deploy as designed based on years of testing and analysis.
“We have found things, and we’ve gone back and corrected them,” he said. “You don’t want to test it too much because the sunshield is so fragile, but we did three or four deployments and the last one, we were fully successful, we felt really good about it. It only has to work one more time. And that’s in orbit.”
HOW DO YOU LAUNCH THE LARGEST MIRROR IN SPACE? FOLD IT UP
Assuming the sunshade does, in fact, deploy normally, the next major challenge will be unfolding JWST’s mirrors starting about 10 days after launch.
The Hubble Space Telescope is a Ritchey-Chrétien Cassegrain, with a 91.5-inch primary mirror and a secondary bringing the light to a sharp focus just behind the main mirror. From there, pick-off mirrors feed the light to the telescope’s instruments.
JWST is what astronomers call a three-mirror anastigmat. Light first hits the 21.3-foot primary mirror, bounces up to the convex secondary and then down, slightly off axis, to a third elliptical mirror just behind the primary. The elliptical mirror corrects for astigmatism and widens the field of view, bouncing the light back up to a flat “steering mirror” that reflects it back down to the instruments.
The steering mirror can tip and tilt “very slightly at up to 100 cycles a second,” Geithner said, to exactly counteract any residual mechanical jitter in the system due to spinning reaction wheels and cryocooler pumps in the spacecraft bus.
Because a one-piece primary mirror would be too heavy and would not fit into an existing nose cone fairing, the observatory was designed around a segmented beryllium primary made up of 18 hexagonal sub-mirrors, each one 4.3 feet in diameter and coated with a thin layer of gold to maximise reflectivity.
Six of those segments, three on each side, were designed to be folded away for launch as was the telescope’s 2.4-foot secondary mirror. About 10 days after launch, after the sunshade is fully deployed and tensioned, Webb’s secondary mirror will be erected at the apex of three articulating booms.
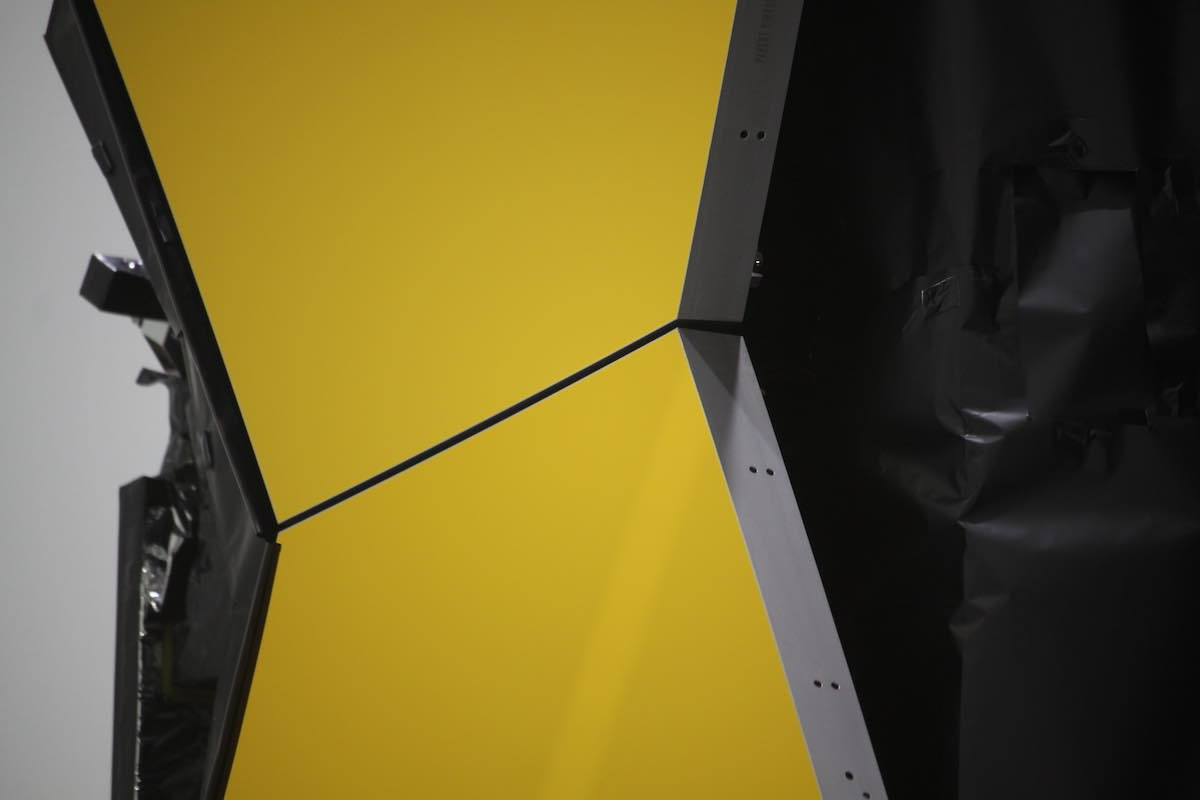
The two side panels of the primary, each with three mirror segments, then will be rotated into position to either side of the central 12 segments.
“The aperture (width) had to be at least six-and-a-half meters (21.3 feet) to gather enough light and have the same resolution at near infrared wavelengths that Hubble has at visible wavelengths,” Geithner said.
Ultra-precise optical alignment of the 18 primary mirror segments is critical. To achieve that, each segment features six mechanical actuators allowing movement in six directions. A seventh actuator can push or pull on the center of a segment to ever so slightly distort its shape if needed.
Each segment was so precisely ground and polished that if one was blown up to the size of the United States, the 14,000-foot-high Rocky Mountains would be less than 2 inches high.
Because the mirror segments will change shape slightly as the telescope cools down in space, “we basically had to build this thing perfectly wrong at room temperature so that it will be precisely correct at an operating temperature below 60 Kelvin,” Geithner said. “That’s the over-arching big challenge.”
Before alignment, the 18 segments will produce 18 separate images. Using the NIRCam instrument, engineers will map the alignment of each segment and send commands to adjust the orientation and curvature as required to produce a single, sharply-focused image.
“You’ve got to get these 18 mirrors to act as one mirror,” Ochs said. “So when we get on orbit, we go through what we call a wavefront sensing process, but really it’s the focusing process. When you start out, if you’re looking at one star, you’re going to have 18 images and you need to get that down to one.
“So we use the actuators on the back of the mirror, there are motors on the back of each mirror that allow you to move the mirrors up and down, back and forth, in and out as well as change shape slightly.”
LEARNING A LESSON FROM HUBBLE
The Hubble Space Telescope was launched in 1990 with a famously flawed primary mirror, the result of a testing error on the ground that led to spherical aberration and blurred pictures. Shuttle astronauts were able to repair the telescope by installing instruments with built-in corrective optics.
With that lesson in mind, JWST managers opted for detailed pre-launch testing to ensure Webb’s optical system will work as planned. Along with exhaustive testing of each primary mirror segment, the entire telescope was sent to the Johnson Space Center in Houston and tested inside an Apollo-era vacuum chamber that duplicated the space environment.
“We made artificial stars with light coming from the end of fibre optics and we passed light all the way through the system and we know we can line it up and make it work,” Geithner said.
And what if an actuator fails or some other problem crops up and one of the primary mirror segments cannot be properly aligned?
“We can meet all our most fundamental requirements with 17 segments,” he said. “We can try to compensate with the other segments and the secondary, it depends on if it’s within a certain range. But if it’s a bad segment, we can just tilt it completely out of the way with the remaining actuators. That’s not great … but we could still meet our level-one requirements.”
When you subscribe to the SpaceZE News Feed, we will send you an e-mail when there are new updates on the site so you wouldn't miss them.